Hand-made ceramics using Renaissance-era techniques in Umbria
From Deruta in Umbria to Crookwell in NSW, Marg Anderson and Jan Pont, along with their good friends Mike and Marguerite Walsh, import Australia’s largest range of glazed Italian earthenware through Paradiso Ceramics.
Deruta ceramics are eye-catching, vibrant, and made using quality craftsmanship. Deruta is a medieval hill town in Perugia, the capital city of Umbria, Italy’s green heart. Umbria is the only region in Italy that does not border the sea or another country. The region is known for its lush green landscapes and local cuisine, and the town of Deruta has long been known as a center for Italian ceramics. Deruta ceramics are part of the tradition of glazed Italian earthenware known as maiolica.
The peak era for Italian ceramics was during the early Renaissance period in the 15th century. Italian ceramics from this period were known as istoriato ware because they were painted with stories depicting historical and mythical scenes. By the late 15th century, multiple locations, mainly in northern and central Italy, were producing high-quality pieces for a sophisticated market in Italy and across the globe. Deruta ceramics were among the most prized in Italy.
In Deruta, the artisans create the maiolica using centuries-old techniques, including throwing clay on a potter’s wheel, carefully hand-molding each piece, and painting intricate and colorful designs. Marg Anderson explains, “You can see the brush strokes where the artists have hand-painted their intricate designs.”
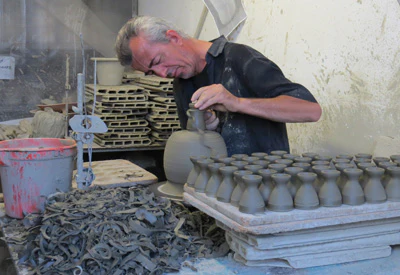
Marg and Jan Pont first fell in love with Italian ceramics during a holiday to Italy in 2006. Since then, the pair have returned to Deruta many times to purchase ceramics for their home, including a dinner set, lamps, bowls, and jugs. After some time, their friends Mike and Marguerite Walsh suggested teaming up to import Deruta ceramics. The pair were delighted by the suggestion and hopped on a plane to Deruta for a buying spree. They came back with stunning maiolica, and Paradiso Ceramics was launched in December 2017. Today, the team imports Australia’s largest range of glazed Italian earthenware. Their 20-hectare property in Crookwell, NSW, includes a showroom. Customers can view the Paradiso Ceramics range of serving ware, homewares, and lava stone tables and collect pieces by appointment.
We are passionate about the beauty of these products and helping artists in this small Umbrian town continue to ply their ancient craft. We carefully select objects that convey the hand-crafted element in the shapes, textures, and colours of the finished works. It is a true privilege to work with these artisans and help them continue to ply their ancient crafts.
The creative process of making maiolica remains the same as it was 500 years ago. To create a single piece of maiolica requires a lengthy five-step process:
STEP 1: MOLDING THE CLAY
A potter throws a lump of refined clay on a wheel, skillfully shaping it into the various canonical forms associated with the tradition. Depending on the piece, a mold or press may also be used to shape the clay. The piece is then left to naturally air dry for up to three days. Once dry, it becomes light grey. At this stage, it is ready for its first firing in the kiln.
STEP 2: FIRST FIRING
The dried piece is cleaned and sanded to remove any imperfections. It is loaded onto a large rack and wheeled into the kiln for firing. The first firing occurs at about 1000 degrees Celsius. After firing, the kiln must remain closed for many hours, allowing the temperature to cool gradually. A dramatic drop in temperature can cause thermal shock and crack the delicate pieces. When fired, the pieces take on the classic terracotta colour and are now referred to as biscotto (bisque or biscuit). The pieces are still porous and fragile at this stage and need to be glazed to turn them into functional pieces of art.
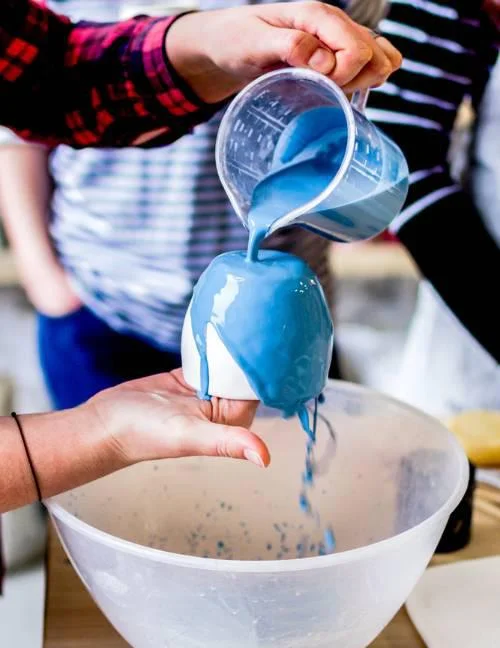
STEP 3: GLAZING
Once cooled, the unfinished pottery pieces are dipped into a bath of fast-drying liquid glaze (typically white or cream). Now wholly covered by the glaze, the biscotti are ready for painting. This glaze layer prevents the colours from spreading and blurring into each other during the painting process.
STEP 4: PAINTING
Artisans use several techniques to paint the pieces. The artist may paint the motifs free-hand. Complex designs can be transferred onto the piece using a paper stencil. Sticks of carbon are gently tapped onto a paper stencil to produce a fine powder, marking the contours of the designs through tiny holes in the paper. Sometimes, the paints used to produce the colors are quite different from the colors that appear after the final firing, as chemical processes occurring at high temperatures change the appearance of the glaze radically. Ceramicists need to understand how the firing will affect their glazes and work accordingly–skill and knowledge gained over many years of experience.
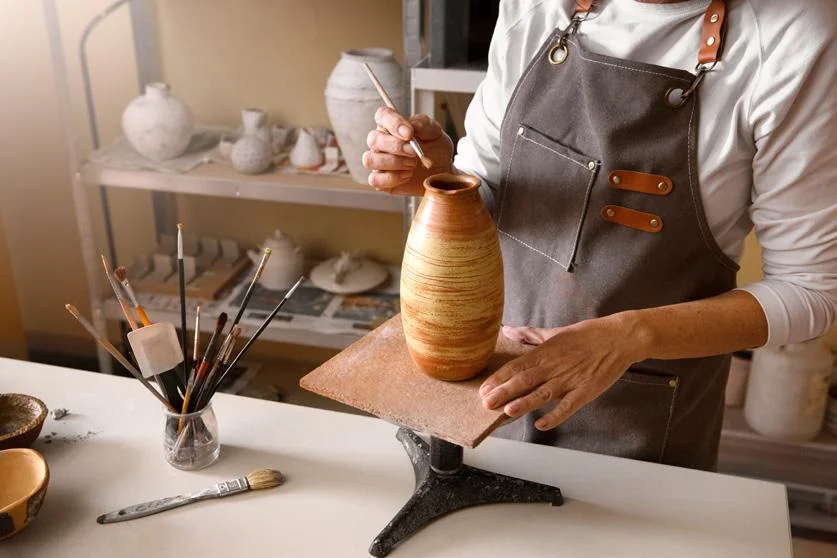
STEP 5: FINAL FIRING
The painted ceramics are again loaded into the kiln for a final firing. The second firing occurs at around 950 degrees Celsius. This delicate process requires great care to avoid scratching any item to be fired. The final firing may take up to 24 hours, with more than 12 hours of constant extreme heat. Like the first firing, it is necessary to let the kiln cool down naturally to avoid cracks from forming.
Marg explained that in Deruta, there is a school where students can learn the traditional techniques of making maiolica as well as how to paint intricate patterns. Six designs form the foundation of Italian ceramics or classic Deruta designs, and they are Antico Deruta, Bordato, Orvieto, Raffaellesco, Ricco Deruta, and Siena.
Marg explained that as you wander through the charming streets of Deruta, “you can see a lot of cafes with lava stone tables. Some will have platters as serving wear. The houses that we stay in are full of maiolica. It’s part of the way that the older generation lives."
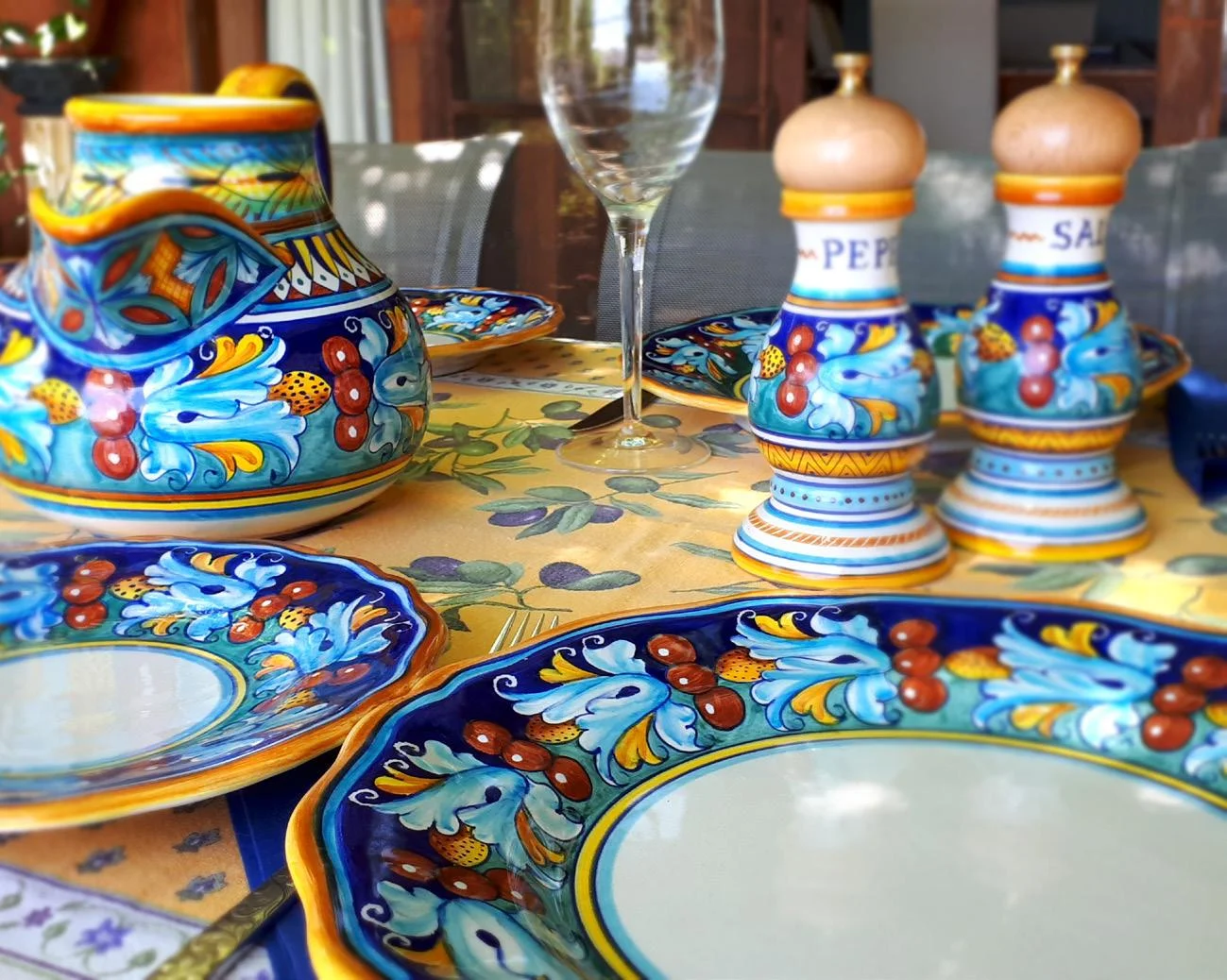
Deruta is part of the organization I Borghi più belli d’Italia (the most beautiful villages in Italy). The organization seeks to preserve small Italian towns with immense historical, artistic, and cultural heritage. It also promotes food and wine traditions, religious and secular festivals, and beautiful landscapes.
Cover image: Paradiso Ceramics, Table on terrace set with Giglio plates
Images provided by Paradiso Ceramics